Knowledge for the workshop world
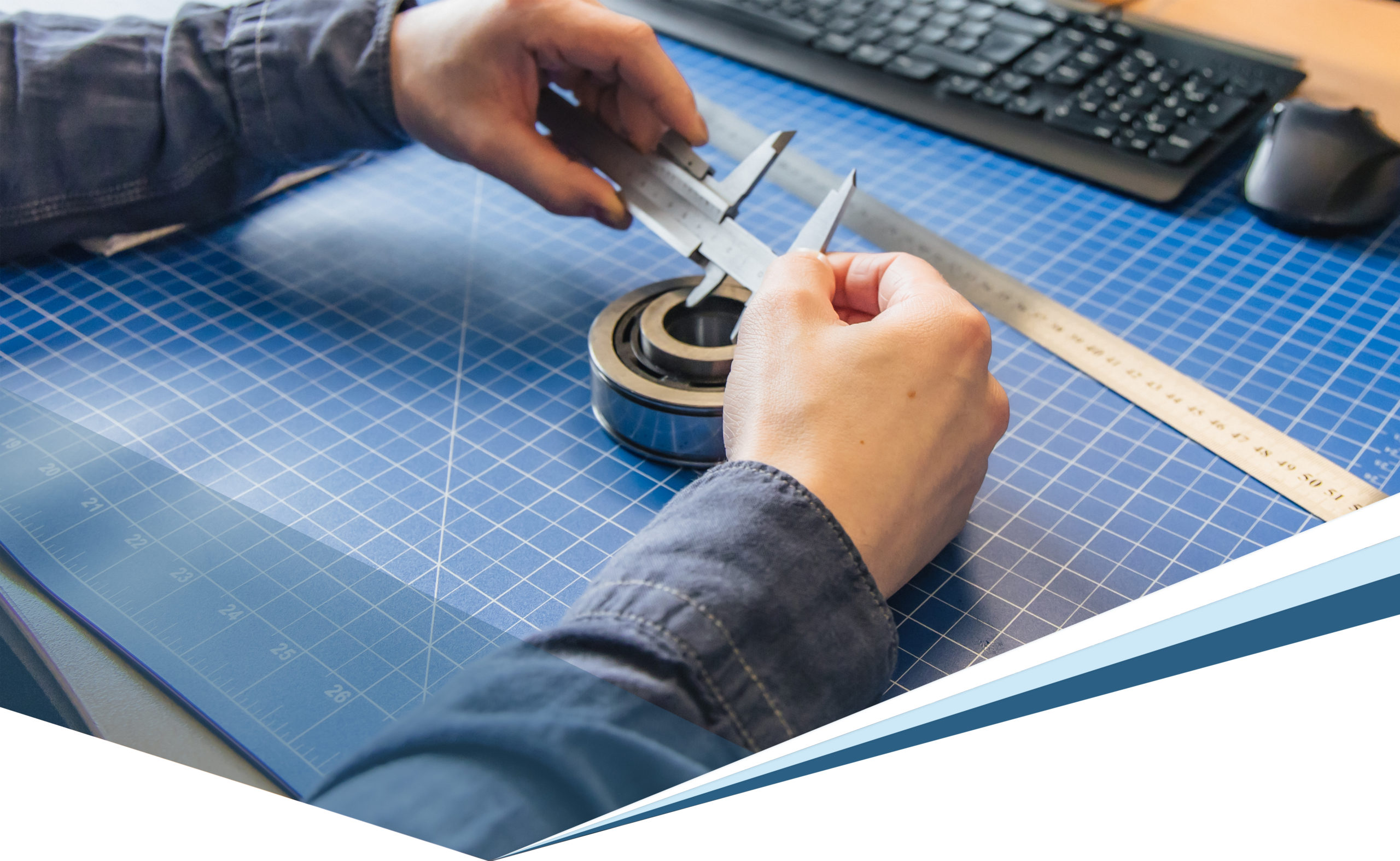
Where know-how is created
The knowledge that workshop professionals need today to do a good job is considerable. The technical editorial team at Trainmobil works daily on solutions to convey the necessary know-how to workshops even more easily and quickly.
Few things are more memorable than the feeling of wiping the chalk off the blackboard with a dry sponge when you were at school. Today, however, we can hardly recall what was written on the blackboards. It doesn’t matter how long ago we left school – whether it was forty, fourteen or four years ago: despite all the technological progress, chalk, blackboard and sponge are still the measure of all things in educational institutions. “The world has moved on – but in many places, it seems that knowledge transfer has not,” explains Markus Guinand, Head of Technical Editing at Trainmobil. “We want to counteract this and make knowledge as accessible as possible. There can’t be just one way to impart know-how.” In short, we live in a world in which we can send large amounts of information around the world in the fraction of a second via data highways. We use smartphones, tablets and computers to access knowledge in real time. We can use learning media that literally immerse ourselves in new realms of knowledge. Of course, we take advantage of all these opportunities to transfer knowledge!
More than just writing
In Trainmobil’s technical editorial department, more than ten employees are now responsible for presenting and communicating knowledge in a tangible way. “When you think of an editorial team, the first thing you think of is a person who writes all day long,” says Guinand. “That’s not wrong at first glance. For example, our editors are responsible for ensuring that the trainers always have up-to-date training material to hand for their courses. For the editorial team, this means: research, research, research.” Like a traditional journalist, the Trainmobil editor starts by sifting through dense data material from a wide variety of sources, sifting out, digging deeper, condensing information – until he ends up with a mountain of knowledge that he can now package in such a way that it is understandable and stays in the heads of the learners . Traditionally, this knowledge is also processed in printed form, for example in the now more than 15 different editions of the specialist series “so geht’s”/”How it works”, which aim at workshop professionals with different topics.“
All of our technical editors have a workshop background, so they already know a lot about car technology. However, their lengthy research inspecialist topics makes them real specialists in these various fields – and we like to make use of this outside of the traditional on-site training and brochures,” says Guinand. “For example, most of our editors regularly offer online training courses on the topics they are particularly well-versed in.” These training courses, which are now also offered internationally, usually last an hour. The editors present them from a modern green screen studio at the Trainmobil headquarters in Hamburg. Videos, animations and graphics can be displayed here at the touch of a button. “This brings the lessons to life. It’s important to us that we don’t do traditional frontal teaching. That’s why, for example, participants can also exchange ideas, ask questions and complete varied tasks during the online training sessions,” says Guinand. “In future, we want to integrate the free Trainmobil app even more, for example for small surveys or a quick quiz in between.”
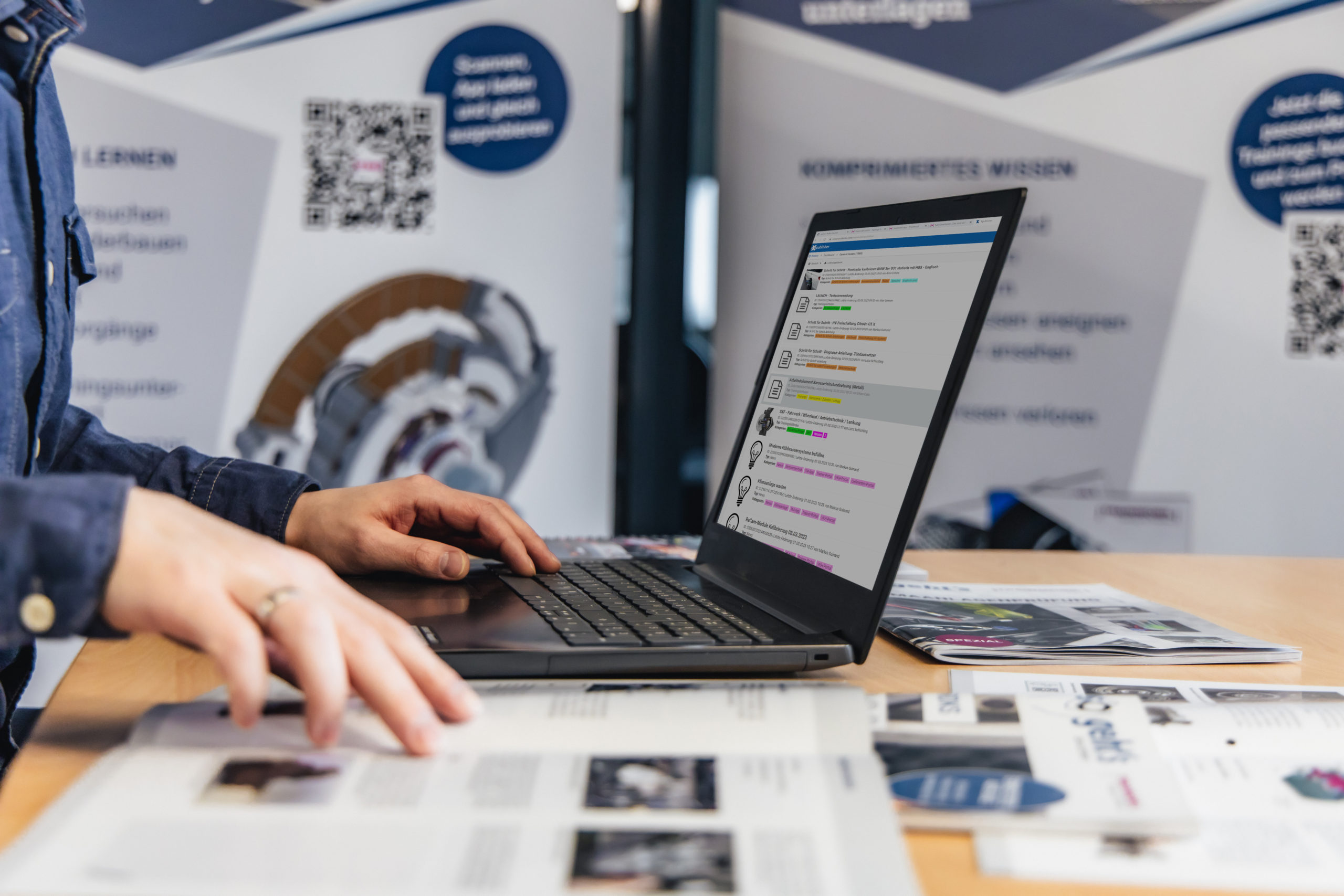
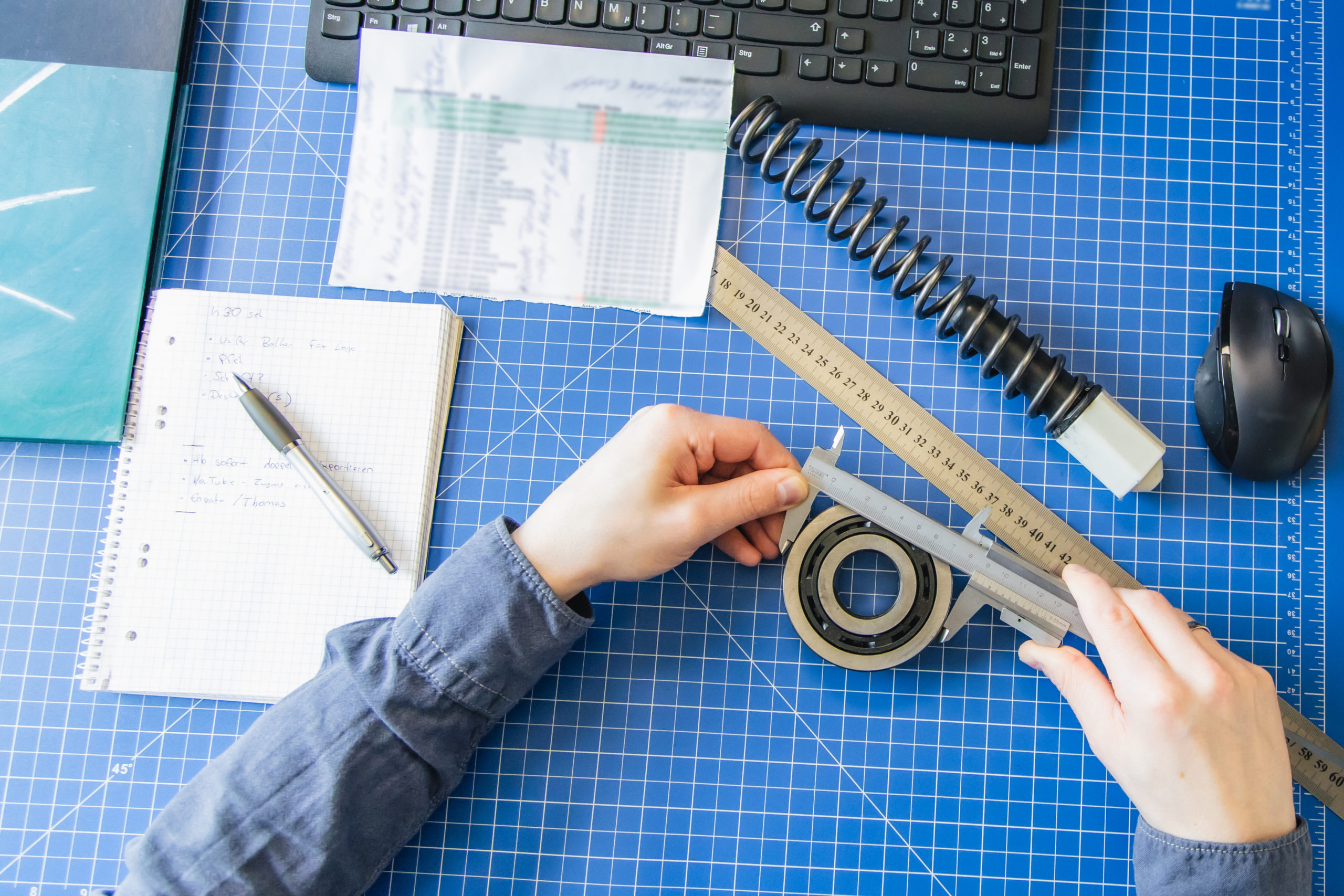
The future in 3D
Teaching material is the linchpin of good training. And it’s not just about comprehensibly written and spoken texts. In order to make knowledge accessible, said multimedia content is particularly important. That’s why Trainmobil’s technical editorial team not only includes traditional editors, but also an entire team that creates graphics, illustrations, technical drawings, 3D models and videos. “None of our products are ready-made,” says Guinand. “We create most of the multimedia content ourselves, from simple graphics and complex illustrations to video tutorials lasting several minutes. It’s quite time-consuming, but we realize with every training session that the work we put in is well worth it.” One example for this is undoubtedly the detailed 3D models and animations that come from Trainmobil. These are based on manually measured components, which are then recreated as virtual models. For learning purposes, these models are even more practical than real components, as the learner can rotate them 360 degrees with the swipe of a finger, zoom in on them continuously and hide or show individual parts. The collection ranges from a simple plug-in connection to the precisely reproduced power electronics of an electric vehicle, which took over 500 hours to create. Trainmobil has recreated more than 20,000 elements to date. With the help of augmented reality, not only can these models be viewed on a screen, but with the Trainmobil app, users can place the virtual elements in real space and literally immerse themselves in the component.
Whether online or onsite, Trainmobil also wants to focus more on 3D in the future of training, and not only for the models, but also for the learning environment. Virtual reality is of the essence here. Whether with the use of VR glasses or via an application on the computer, learners enter a digital learning world, for example in the completely virtualized training workshop at Trainmobil. Here you have a myriad of possibilities. Try things out safely, simulate, change the framework conditions, and all that at the click of a mouse. “Learners can really only have such unrestricted hands-on opportunities in the virtual world,” explains Guinand. “You can never have every engine model with you during a training seminar in the real world. And you can’t just flex a gearbox at every training session to take a look at a small oil bore. In the VR world, all of this is possible without any problems. All in all, complex issues can be explained particularly easily.”
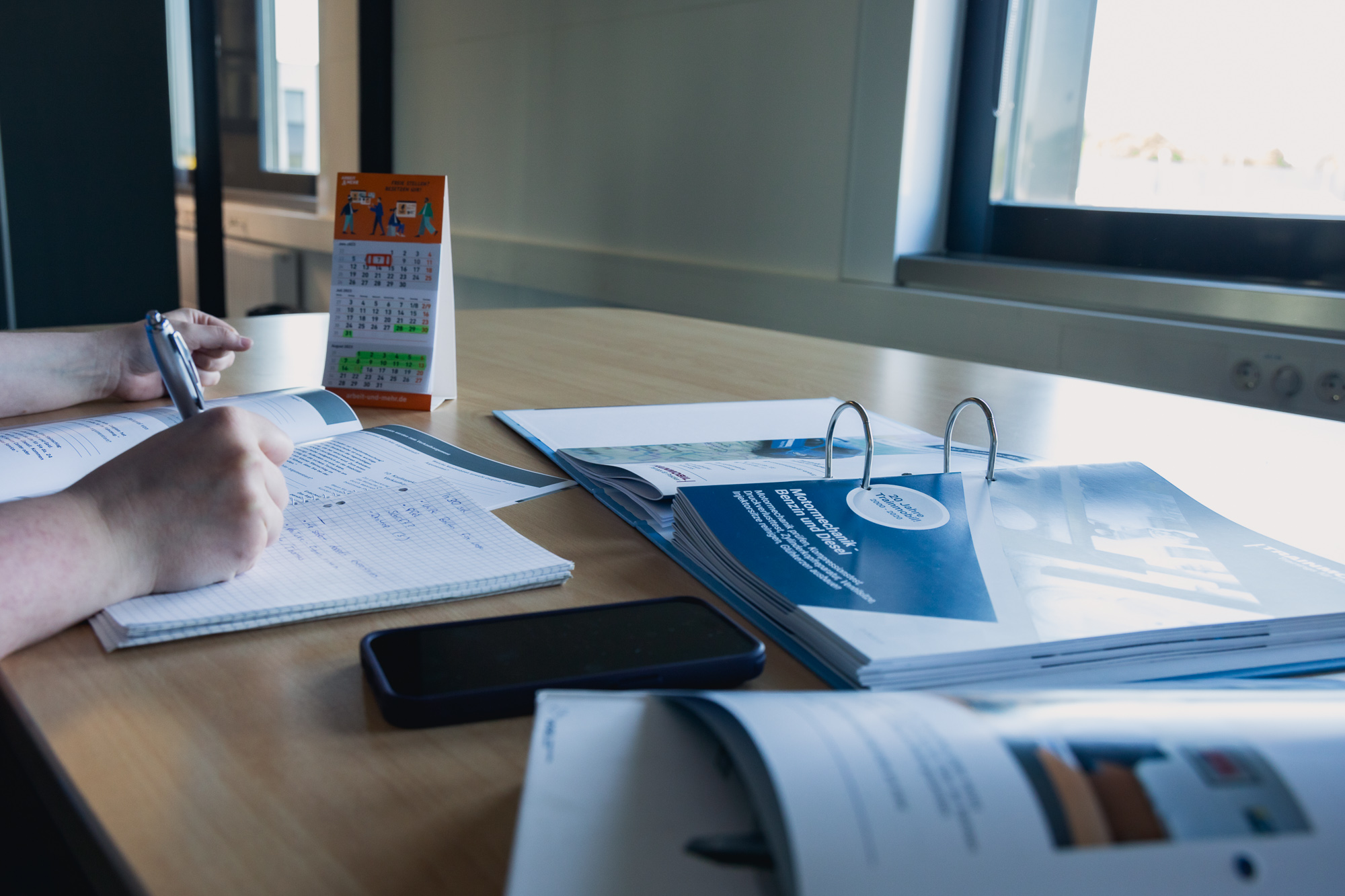
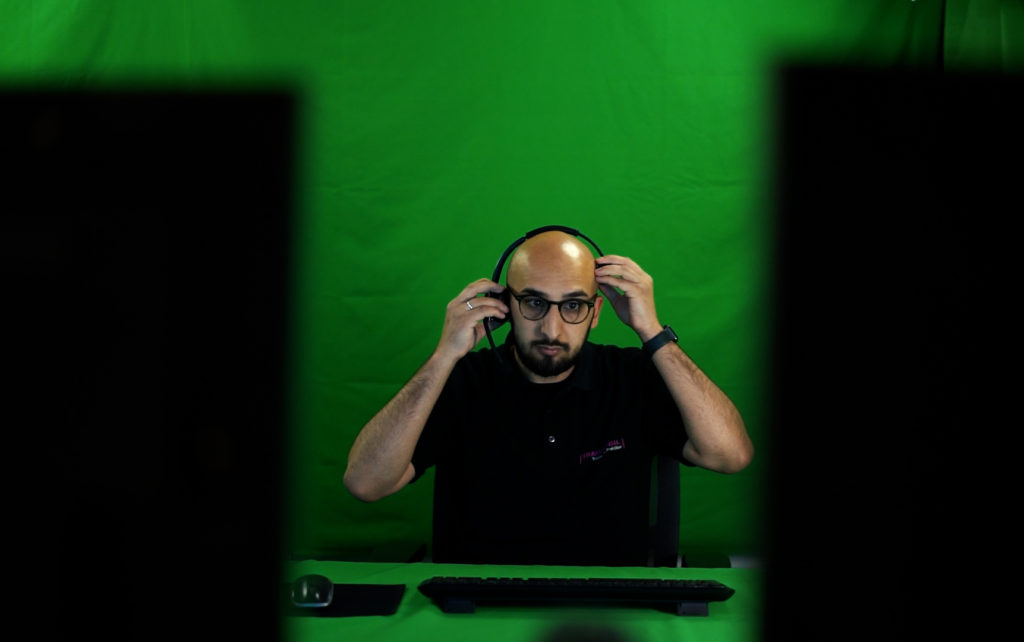
KNOWLEDGE AT YOUR FINGER TIPS
As vehicle technology becomes ever more complex, there is also a change in know-how in the market. The master craftsman who has an answer to every question no longer exists. Basic understanding, acquired in training courses and in practice, is of course still essential. However, for the concrete challenges of everyday life today, more information is often simply needed. And this is where technical editing comes in.“ The most exciting products for the workshop market is certainly our online repair manuals,” says Guinand. “These are guides that lead the workshop professional step by step through repairs and service work.” Each guide begins by stating how long the work will take, how complex the process is and which tools are required. This is followed by detailed descriptions of the individual steps, also enriched by videos, zoomable graphics and interactive 3D models. So, you literally have the knowledge you need at your fingertips in the workshop, on your smartphone or tablet, directly on the vehicle. Almost 50 instructions on a wide range of topics are already available for download in German and English, and range from camera calibration and high-voltage activation to maintaining digital service booklets. The number is set to grow to 150 by the end of this year.
We all agree that it is not possible to pack all the knowledge of the technical editorial team at Trainmobil into words, graphics, videos and 3D models. There are so many exceptions to the rules that make everyday workshop life so exciting.“ And we also want to help workshops in these cases by ensuring that the technical editors can also respond to individual inquiries,” explains Guinand. “One way of doing this is via the classic hotline, which more and more workshops are now using when they get stuck on a topic. Admittedly, even our editors occasionally have to do some research or try out different repair methods in our workshop, but so far we have always found a solution.” Another Trainmobil tool that companies can use is remote diagnostics. A remote diagnostics technician connects directly to the vehicle in the workshop via the internet. There he can carry out tasks like reading out error codes, flashing control units, calibrating camera and radar systems, just to name a few.
The market recognizes the signs of the times
Anyone looking at the portfolio of technical editors at Trainmobil may well wonder whether there is a more varied job in Hamburg. “I can’t think of one,” says Guinand with a smile. “On the contrary, we don’t want to stand still and are always looking for new ways to bring specialist knowledge to the market in a sustainable way. Incidentally, this now also applies to more and more industrial customers from the sector, be it via an individualized hotline, branded online repair instructions or technical training, which we tailor precisely to customer requirements with our self-developed presentation tool. More and more companies are simply realizing that the clear communication of know-how is one of the biggest added value factors in the market.” Communicating know-how well! Trainmobil can do that! No chalk, no blackboard, no dry sponge!